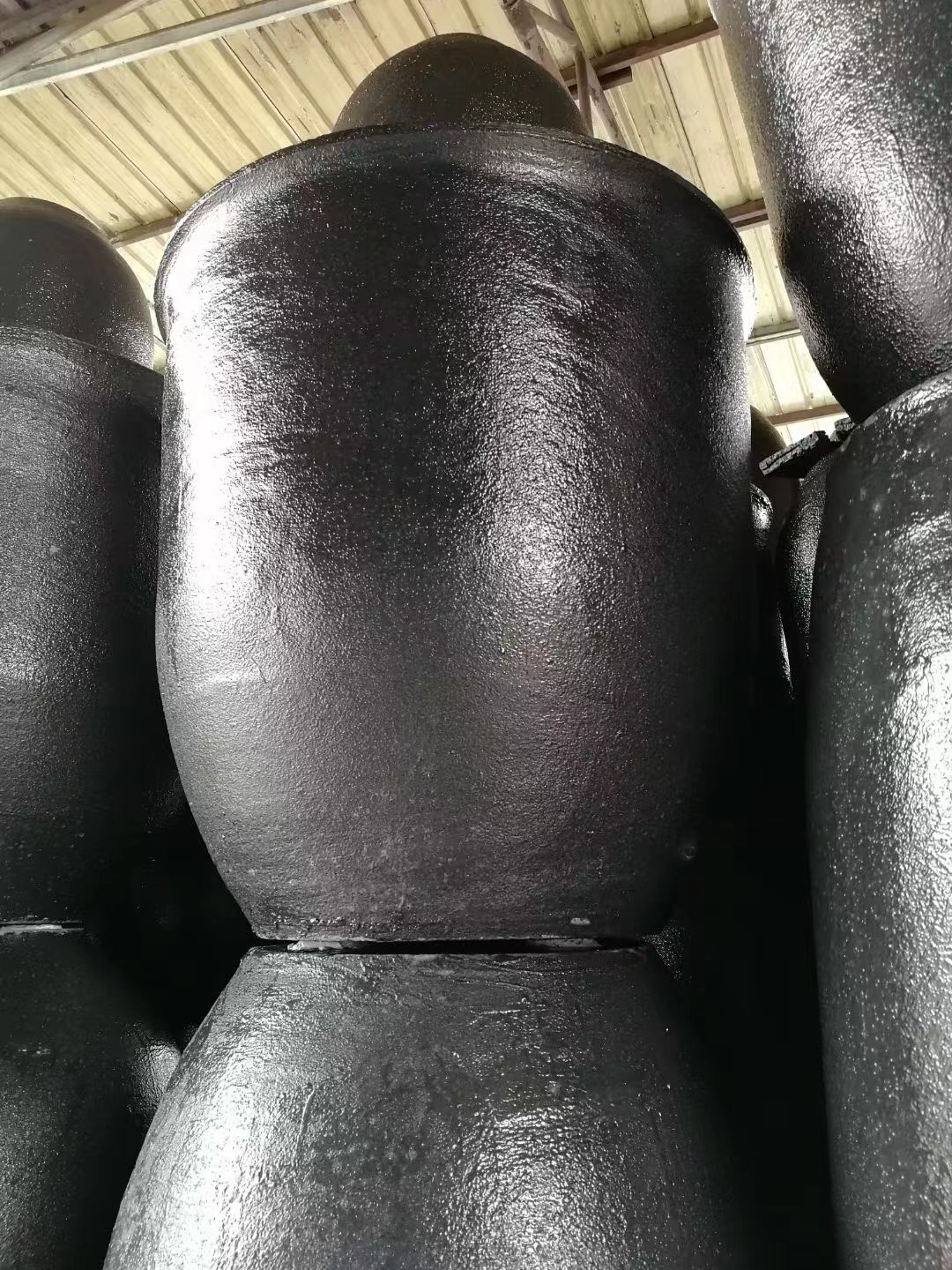
Proper usage and maintenance of silicon carbide crucibles play a vital role in their longevity and effectiveness. Here are the recommended steps for installing, preheating, charging, slag removal, and post-use maintenance of these crucibles.
Installation of the Crucible:
Before installation, inspect the furnace and address any structural issues.
Clear any residues from the furnace walls and bottom.
Ensure the proper functioning of the leakage holes and clear any blockages.
Clean the burner and verify its correct positioning.
Once all the above checks are complete, place the crucible in the center of the furnace's base, allowing a 2 to 3-inch gap between the crucible and the furnace walls. The material at the bottom should be the same as the crucible material.
The burner flame should directly touch the crucible at the joint with the base.
Crucible Preheating: Preheating is crucial to extend the lifespan of the crucible. Many instances of crucible damage occur during the preheating phase, which may not be apparent until the metal melting process begins. Follow these steps for proper preheating:
For new crucibles, gradually increase the temperature by 100-150 degrees Celsius per hour until reaching around 200°C. Maintain this temperature for 30 minutes, then slowly raise it to 500°C to remove any absorbed moisture.
Subsequently, heat the crucible to 800-900°C as quickly as possible and then lower it to the working temperature.
Once the crucible temperature reaches the working range, add small quantities of dry material to the crucible.
Charging the Crucible: Proper charging techniques contribute to the longevity of the crucible. Avoid placing cold metal ingots horizontally or throwing them into the crucible under any circumstances. Follow these guidelines for charging:
Dry the metal ingots and larger chunks before adding them to the crucible.
Place the metal material loosely in the crucible, starting with smaller pieces as a cushion and then adding larger chunks.
Avoid adding large metal ingots to a small quantity of liquid metal, as it may cause rapid cooling, resulting in metal solidification and potential crucible cracking.
Clean the crucible of all liquid metal before shutting down or during extended breaks, as different expansion coefficients of the crucible and metal may lead to cracking during reheating.
Maintain the molten metal level in the crucible at least 4 cm below the top to prevent overflow.
Slag Removal:
Add slag-removing agents directly to the molten metal and avoid introducing them into an empty crucible or mixing them with the metal charge.
Stir the molten metal to ensure even distribution of the slag-removing agents and prevent them from reacting with the crucible walls, as this can cause corrosion and damage.
Clean the crucible interior walls at the end of each workday.
Post-Use Maintenance of the Crucible:
Empty the molten metal from the crucible before shutting down the furnace.
While the furnace is still hot, use suitable tools to scrape off any slag adhering to the crucible walls, taking care not to damage the crucible.
Keep the leakage holes closed and clean.
Allow the crucible to cool naturally to room temperature.
For occasionally used crucibles, store them in a dry and protected area where they are less likely to be disturbed.
Handle the crucibles gently to avoid breakage.
Avoid exposing the crucible to air immediately after heating, as this may cause
Post time: Jun-29-2023