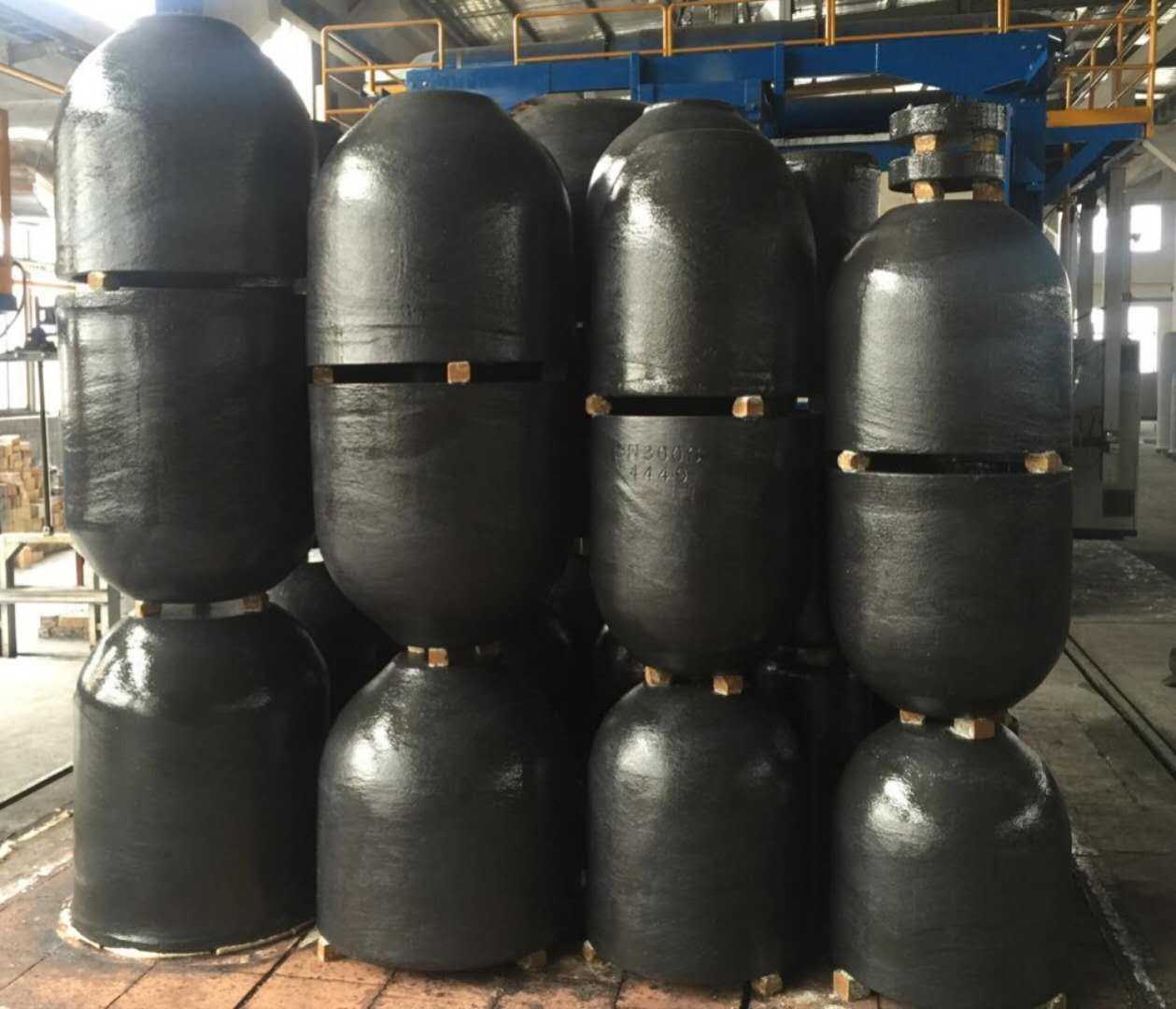
In pursuit of maximizing the lifespan and utilizing the characteristics of graphite crucibles, our factory has conducted extensive research and exploration in their production and operation. Here are the operating instructions for graphite crucibles:
Special precautions for high-purity graphite crucibles:
Avoid mechanical impacts and do not drop or strike the crucible from a height. And keep it dry and away form moisture. Don’t touch water after it has been heated and dried.
When using, avoid directing the flame directly onto the crucible's bottom. Direct exposure to the flame can leave significant black marks.
After shutting down the furnace, remove any remaining aluminum or copper material from the crucible and avoid leaving any residue.
Use acidic substances (such as flux) in moderation to prevent corroding and cracking of the crucible.
When adding materials, avoid hitting the crucible and refrain from using mechanical force.
Storage and transfer of graphite crucibles:
High-purity graphite crucibles are sensitive to water, so they should be protected from dampness and water exposure.
Pay attention to avoiding surface damage. Do not place the crucible directly on the floor; instead, use a pallet or stack board.
When moving the crucible, avoid rolling it sideways on the floor. If it needs to be rotated vertically, place a thick cardboard or cloth on the floor to prevent scratches or abrasions on the bottom.
During transfer, take special care not to drop or strike the crucible.
Installation of graphite crucibles:
The crucible stand (crucible platform) should have the same or larger diameter as the crucible's bottom. The height of the platform should be higher than the flame nozzle to prevent the flame from reaching the crucible directly.
If using refractory bricks for the platform, circular bricks are preferred, and they should be flat without any bending. Avoid using half or uneven bricks, and it is recommended to use imported graphite platforms.
Place the crucible stand at the center of melting or annealing, and use carbon powder, rice husk ash, or refractory cotton as a cushion to prevent the crucible from sticking to the stand. After placing the crucible, ensure it is leveled (using a spirit level).
Choose the fit crucibles which is compatible with the furnace, and keep an appropriate gap(at least (40mm) between the crucible and the furnace wall.
When using a crucible with a spout, leave a space of approximately 30-50mm between the spout and the refractory brick below. Do not place anything underneath, and use refractory cotton to smooth the connection between the spout and the furnace wall. The furnace wall should have fixed refractory bricks (three points), and a corrugated cardboard about 3mm thick should be placed under the crucible to allow for thermal expansion after heating.
Preheating and drying of graphite crucibles:
Preheat the crucible near an oil furnace for 4-5 hours before use to assist in moisture removal from the crucible's surface.
For new crucibles, place charcoal or wood inside the crucible and burn it for approximately four hours to help remove moisture.
The recommended heating times for a new crucible are as follows:
0℃ to 200℃: Slowly raise the temperature over 4 hours.
For oil furnaces: Increase the temperature slowly for 1 hour, from 0℃ to 300℃, and need 4hours from200℃ to 300℃,
For electric furnaces: need 4 hours heating time from 300℃ to 800℃, then 4 hours from 300℃ to 400℃. from 400℃ to 600℃, increase the temperature rapidly and maintain for 2 hours.
After shutting down the furnace, the recommended reheating times are as follows:
For oil and electric furnaces: Need 1 hours heating time from 0℃ to 300℃. Need 4 hours heating time from 300℃ to 600℃. Rapidly increase the temperature to the desired level.
Charging materials:
When using high-purity graphite crucibles, start by adding small corner materials before adding larger pieces. Use tongs to carefully and quietly place the materials into the crucible. Avoid overloading the crucible to prevent it from breaking.
For oil furnaces, materials can be added after reaching 300℃.
For electric furnaces:
From 200℃ to 300℃, start adding small materials. From 400℃ onward, gradually add larger materials. When adding materials during continuous production, avoid adding them in the same position to prevent oxidation at the crucible mouth.
For insulation electric furnaces, preheat to 500℃ before pouring aluminum melt.
Precautions during the use of graphite crucibles:
Handle materials with care when adding them to the crucible, avoiding forceful placement to prevent damaging the crucible.
For crucibles continuously used for 24 hours, their lifespan can be extended. At the end of the workday and furnace shutdown, the molten material in the crucible should be removed to prevent solidification and subsequent expansion, which can lead to crucible deformation or breakage.
When using melting agents (such as FLLUX for aluminum alloys or borax for copper alloys), use them sparingly to avoid corroding the crucible walls. Add the agents when the aluminum melt is about 8 minutes away from being full, gently stirring to prevent them from adhering to the crucible walls.
Note: If the melting agent contains more than 10% sodium (Na) content, a special crucible made of specific materials is required.
At the end of each workday, while the crucible is still hot, promptly remove any metal adhering to the crucible walls to prevent excessive residue, which can affect heat transfer and prolong dissolution time, causing thermal expansion and potential crucible breakage.
It is recommended to check the crucible's condition approximately every two months for aluminum alloys (weekly for copper alloys). Inspect the external surface and clean the furnace chamber. Additionally, rotate the crucible to ensure even wear, which helps extend the lifespan of high-purity graphite crucibles.
By following these operating instructions, users can maximize the lifespan and efficiency of their graphite crucibles, ensuring optimal performance in various applications.
Post time: Jul-10-2023