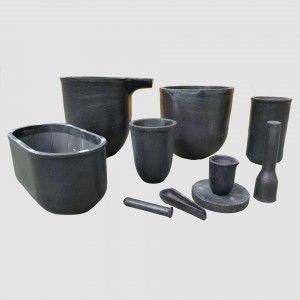
Graphite Carbon Crucible are commonly used tools in metal smelting, laboratory applications, and other high-temperature treatment processes. They have excellent high-temperature stability and thermal conductivity, making them very popular in these applications. This article will delve into how to make Carbon Graphite Crucible, from the selection of raw materials to the manufacturing process of the final product.
Step 1: Select the appropriate graphite material
The first step in making a graphite crucible is to choose the appropriate graphite material. Graphite crucibles are usually made of natural or artificial graphite. Here are some factors to consider when choosing graphite materials:
1. Purity:
The purity of graphite is crucial to the performance of the crucible. High purity graphite crucibles can work stably at higher temperatures and are not easily affected by chemical reactions. Therefore, manufacturing high-quality graphite crucibles usually requires the use of highly pure graphite materials.
2. Structure:
The structure of Graphite Lined Crucible is also a key factor. Fine grained graphite is usually used to manufacture the interior of crucibles, while coarser grained graphite is used to manufacture the outer shell. This structure can provide the required heat resistance and thermal conductivity of the crucible.
3. Thermal conductivity:
Graphite is an excellent thermal conductive material, which is one of the reasons why graphite crucibles are widely used in high-temperature applications. Choosing graphite materials with high thermal conductivity can improve the heating and cooling rates of the crucible.
4. Corrosion resistance:
Depending on the properties of the substance being processed, it is sometimes necessary to choose graphite materials with corrosion resistance. For example, crucibles that handle acidic or alkaline substances typically require graphite with corrosion resistance.
Step 2: Prepare the original graphite material
Once a suitable graphite material is selected, the next step is to prepare the original graphite material into the shape of a crucible. This process typically includes the following steps:
1. Crushing:
The original graphite material is usually large and needs to be crushed into smaller particles for subsequent processing. This can be achieved through mechanical crushing or chemical methods.
2. Mixing and binding:
Graphite particles usually need to be mixed with binding agents to form the original shape of the crucible. Binders can be resins, adhesives, or other materials used to bond graphite particles to maintain a sturdy structure in subsequent steps.
3. Suppression:
The mixed graphite and binder usually need to be pressed into the shape of a crucible under high temperature and pressure. This step is usually completed using a special crucible mold and a press.
4. Drying:
The pressed crucible usually needs to be dried to remove moisture and other solvents from the binding agent. This step can be carried out at a mild temperature to prevent deformation or cracking of the crucible.
Step 3: Sintering and processing
Once the original crucible is prepared, sintering and treatment processes need to be carried out to ensure that the crucible has the required performance. This process typically includes the following steps:
1. Sintering:
The original Crucible usually needs to be sintered at high temperatures to make the graphite particles bond more tightly and improve the density and strength of the crucible. This step is usually carried out under nitrogen or inert atmosphere to prevent oxidation.
2. Surface treatment:
The internal and external surfaces of crucibles usually require special treatment to improve their performance. Internal surfaces may require coating or coating to increase corrosion resistance or improve heat conduction. The external surface may require polishing or polishing to obtain a smooth surface.
3. Inspection and quality control:
Strict inspection and quality control must be carried out during the manufacturing process to ensure that the crucible meets the specification requirements. This includes checking the size, density, thermal conductivity, and corrosion resistance of the crucible.
Step 4: Final processing and finished products
Finally, the crucible prepared through the above steps can be subjected to final processing to obtain the finished product. This includes trimming the edges of the crucible, ensuring accurate dimensions, and conducting final quality checks. Once the crucible passes quality control, it can be packaged and distributed to customers.
In short, making graphite crucibles is a complex process that requires precise craftsmanship and high-quality graphite materials. By selecting appropriate materials, preparing raw materials, sintering and processing, and implementing strict quality control, high-performance graphite crucibles can be produced for various high-temperature applications. The manufacturing of graphite crucibles is an important part of the field of graphite engineering, providing an indispensable tool for various industrial and scientific applications.
Post time: Oct-14-2023