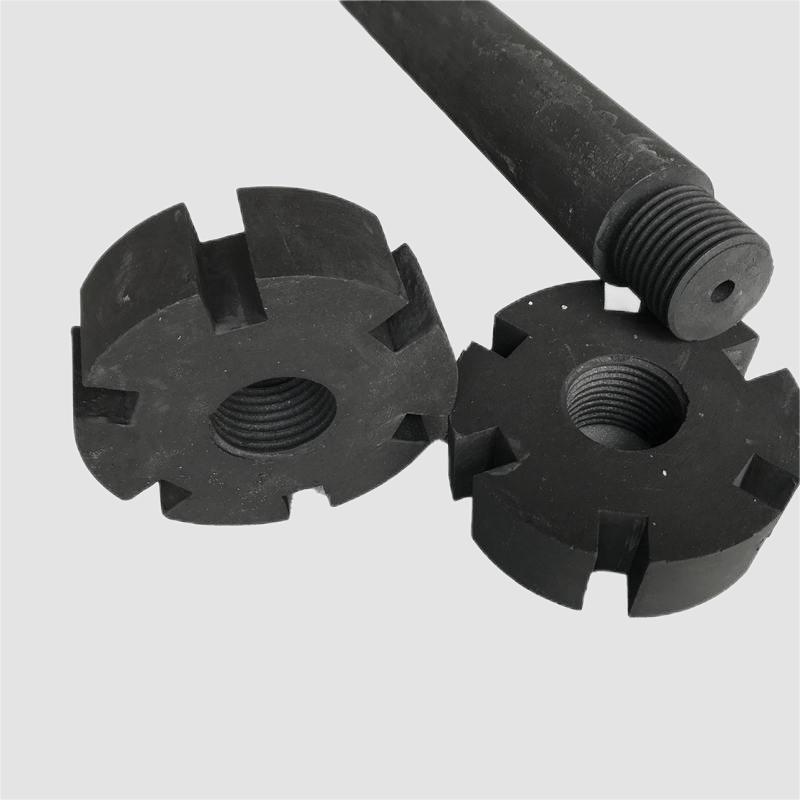
Graphite rotor for aluminum casting is an indispensable auxiliary equipment in the aluminum alloy casting industry, whose function is to purify aluminum melt and improve the quality and stability of aluminum alloy casting. This article will delve into the working principle, advantages, characteristics, and customized solutions of graphite rotors for aluminum casting, in order to help more people understand the importance and application fields of this key device.
Working principle: key to purifying aluminum melt
The main function of graphite rotor for aluminum casting is to inject nitrogen or argon gas into the aluminum melt through rotation, breaking the gas into a large number of dispersed bubbles and dispersing them in the molten metal. Then, the graphite rotor utilizes the gas differential pressure of bubbles in the melt and the principle of surface adsorption to absorb hydrogen gas and oxidation slag in the melt. These bubbles gradually rise with the rotation of the graphite rotor and carry away the adsorbed harmful gases and oxides from the surface of the melt, thus playing a role in purifying the melt. Due to the small and uniform distribution of bubbles in the melt, which are mixed evenly with the melt and do not form a continuous airflow, harmful hydrogen gas in the aluminum melt can be effectively removed, significantly improving the purification effect.
Advantages and characteristics of graphite rotor
Graphite rotors for aluminum casting have many advantages and characteristics in aluminum alloy casting, making them highly favored. Firstly, the rotating nozzle of the graphite rotor is made of high-purity graphite with a special surface treatment, so its service life is usually about three times that of ordinary products. This means that graphite rotors can operate stably for a long time, reducing replacement frequency and labor costs.
Secondly, graphite rotors can reduce processing costs, inert gas consumption, and the aluminum content in the aluminum melt. During the degassing and purification process, through a reasonably designed nozzle structure, the graphite rotor can disperse the bubbles and mix them evenly with the aluminum alloy liquid, increasing the contact area and time between the bubbles and the aluminum alloy liquid, thereby improving the degassing and purification effect.
In addition, the speed of the graphite rotor can be controlled through frequency converter speed regulation, achieving stepless adjustment, with a maximum of 700 r/min. This provides convenience for operation and control during the production process, enabling the degassing rate to reach over 50%, further shortening the smelting time and reducing production costs.
Customized solution: meeting different needs
For the design and ordering of graphite rotors for aluminum casting, due to the different specifications of graphite rotors used in different production lines, technical analysis needs to be conducted based on the original design drawings provided by the customer and the on-site usage environment questionnaire of graphite rotors filled in. Propose a suitable anti erosion treatment plan based on factors such as the rotational speed, direction of rotation, and relative position with the aluminum liquid surface of the graphite rotor. The rotating nozzle of the graphite rotor is made of high-purity graphite, and its structure not only considers the function of dispersing bubbles, but also fully utilizes the centrifugal force generated by stirring the aluminum alloy melt to make the melt enter the nozzle and evenly mix with the horizontally sprayed gas, forming a gas-liquid flow and spraying out, increasing the contact area and contact time between the bubbles and the aluminum alloy liquid, thereby improving the degassing and purification effect.
The graphite rotor has a wide range of specifications and is suitable for Φ 70mm~250mm rotor and Φ Impeller with a diameter of 85mm to 350mm. High purity graphite rotor has the characteristics of high strength, high temperature resistance, and aluminum flow corrosion resistance, which can operate stably in high-temperature environments.
Conclusion
In summary, graphite rotors for aluminum casting play a crucial role in aluminum alloy casting, improving the quality and stability of aluminum alloy casting by purifying the aluminum melt. Graphite rotors have a longer service life and higher degassing and purification efficiency, which can reduce processing costs, inert gas consumption, and aluminum content in slag, improving casting efficiency and production cost-effectiveness. Through reasonable design and selection of appropriate specifications, graphite rotors can meet the needs of different aluminum alloy casting production lines, providing reliable support and guarantee for the development of the aluminum alloy casting industry. With the continuous progress of manufacturing technology, graphite rotors for aluminum casting will continue to play an important role in the field of aluminum alloy casting, driving the continuous development and innovation of this industry.
Post time: Oct-17-2023