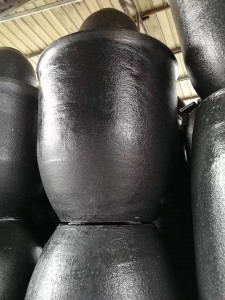
In recent years, the application of graphite crucibles in industrial metal smelting and casting has been steadily increasing, thanks to their ceramic-based design that imparts exceptional high-temperature resistance. However, in practical usage, many overlook the crucial preheating process of new graphite crucibles, leading to potential risks to personal and property safety due to crucible fractures. To maximize the benefits of graphite crucibles, we provide scientifically-based recommendations for their proper use, ensuring both efficient production and industrial safety.
Characteristics of Graphite Crucibles
Graphite crucibles play a vital role in metal smelting and casting due to their outstanding thermal conductivity. While they exhibit better thermal conductivity compared to silicon carbide crucibles, they are susceptible to oxidation and have a higher rate of breakage. To address these issues, it is essential to employ a scientifically sound preheating process.
Preheating Guidelines
- Placement near an Oil Furnace for Preheating: Place the crucible near an oil furnace for 4-5 hours before initial use. This preheating process aids in surface dehumidification, enhancing the crucible's stability.
- Burning of Charcoal or Wood: Place charcoal or wood inside the crucible and burn for approximately four hours. This step assists in dehumidification and improves the crucible's heat resistance.
- Furnace Temperature Ramp-up: During the initial heating phase, gradually increase the temperature in the furnace based on the following temperature stages to ensure stability and longevity of the crucible:
- 0°C to 200°C: Slow heating for 4 hours (oil furnace) / electric
- 0°C to 300°C: Slow heating for 1 hour (electric)
- 200°C to 300°C: Slow heating for 4 hours (furnace)
- 300°C to 800°C: Slow heating for 4 hours (furnace)
- 300°C to 400°C: Slow heating for 4 hours
- 400°C to 600°C: Rapid heating, maintaining for 2 hours
- Post Shutdown Reheating: After shutting down, the reheating time for oil and electric furnaces is as follows:
- 0°C to 300°C: Slow heating for 1 hour
- 300°C to 600°C: Slow heating for 4 hours
- Above 600°C: Rapid heating to the required temperature
Shutdown Guidelines
- For electric furnaces, it is advisable to maintain continuous insulation when idle, with the temperature set around 600°C to prevent rapid cooling. If insulation is not possible, extract materials from the crucible to minimize residual content.
- For oil furnaces, after shutdown, ensure to scoop out materials as much as possible. Close the furnace lid and ventilation ports to preserve residual heat and prevent crucible moisture.
By adhering to these scientifically grounded preheating guidelines and shutdown precautions, the optimal performance of graphite crucibles in industrial production can be ensured, simultaneously enhancing production efficiency and safeguarding industrial safety. Let us collectively commit to technological innovation to drive industrial progress.
Post time: Dec-04-2023