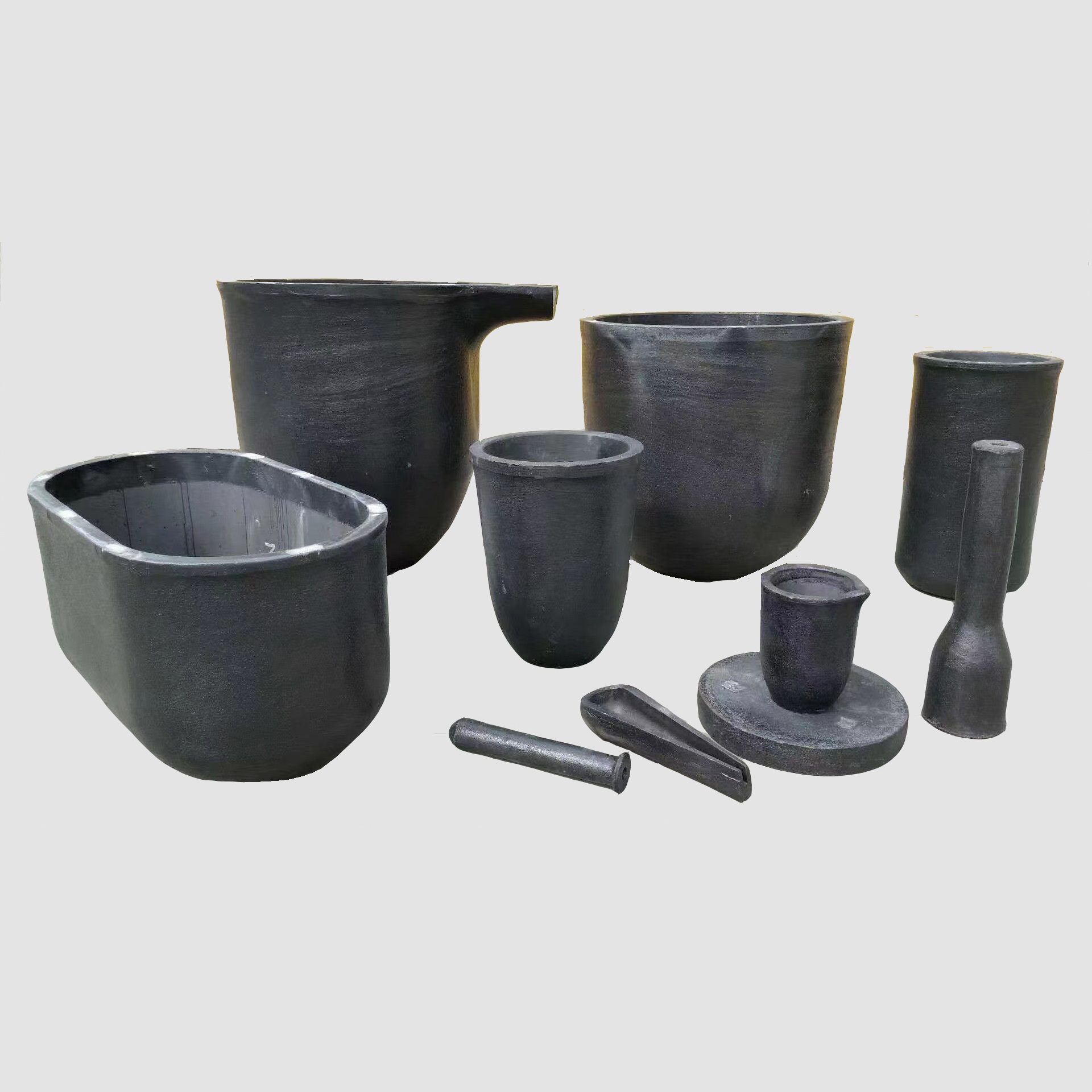
In recent years, the production technology of domestic graphite crucibles has made significant progress. Not only have they caught up with imported crucibles, but in some cases even exceeded them. By employing innovative manufacturing techniques and sourcing high-quality raw materials, graphite crucibles can now withstand extreme conditions with unparalleled efficiency.
The main features of these new graphite crucibles are undoubtedly worth noting. First, they have high thermal conductivity, significantly reducing melting time, thanks to the use of raw materials such as graphite, which has excellent thermal conductivity. This increase in efficiency not only saves time and energy, but also increases productivity across industries.
In addition, these crucibles have excellent heat resistance and can withstand temperatures up to 1200 to 1600°C. This exceptional quality makes it ideal for applications requiring high temperatures, such as metal castings and foundries. The ability to withstand such extreme temperatures without compromising performance is a game-changer for many industrial processes.
One of the most remarkable properties of these graphite crucibles is their excellent corrosion resistance. They show great resistance even in the face of highly corrosive molten materials, ensuring longevity and enhanced performance. This corrosion resistance expands the range of applications of these crucibles, especially in the chemical and metallurgical industries.
Additionally, its superior thermal shock resistance makes it superior to similar products. Graphite crucibles exhibit elasticity under rapid cooling and heating cycles, making them less susceptible to cracking and breakage. This superior durability not only improves safety but also provides significant cost savings by reducing the need for frequent replacements.
Graphite crucibles are widely used in various industries due to their excellent thermal conductivity and high temperature resistance. These crucibles have a low coefficient of thermal expansion and are resistant to sudden changes in temperature. They can withstand rapid heating and cooling without suffering major strains, ensuring optimal performance and reliability.
Graphite crucibles have exemplary corrosion resistance to acidic and alkaline solutions, making them vital in laboratories and chemical manufacturing plants. Their excellent stability to chemical reactions demonstrates their durability and can safely handle a wide range of chemicals.
The composition of graphite crucible is natural flake graphite as the main raw material. It is held together using a special adhesive called plastic fire charcoal. This unique combination ensures that graphite crucibles maintain structural integrity under harsh conditions, providing consistent results in a variety of applications.
The advent of domestically produced graphite crucibles not only marks a technological breakthrough, but also supports the development of local industries. Locally manufactured, high-quality crucibles reduce reliance on imports while providing competitive prices for a range of businesses. This development paves the way for greater self-sufficiency and strengthens the country’s industrial landscape.
In summary, innovations in graphite crucible production have pushed it to new heights, surpassing similar imported products in terms of performance and durability. Excellent thermal conductivity, excellent heat resistance, corrosion resistance and thermal shock resistance make it invaluable in a variety of industrial applications. With these advancements, the domestic graphite crucible industry has made significant contributions to the country's industrial growth and self-reliance.
Post time: Oct-08-2023