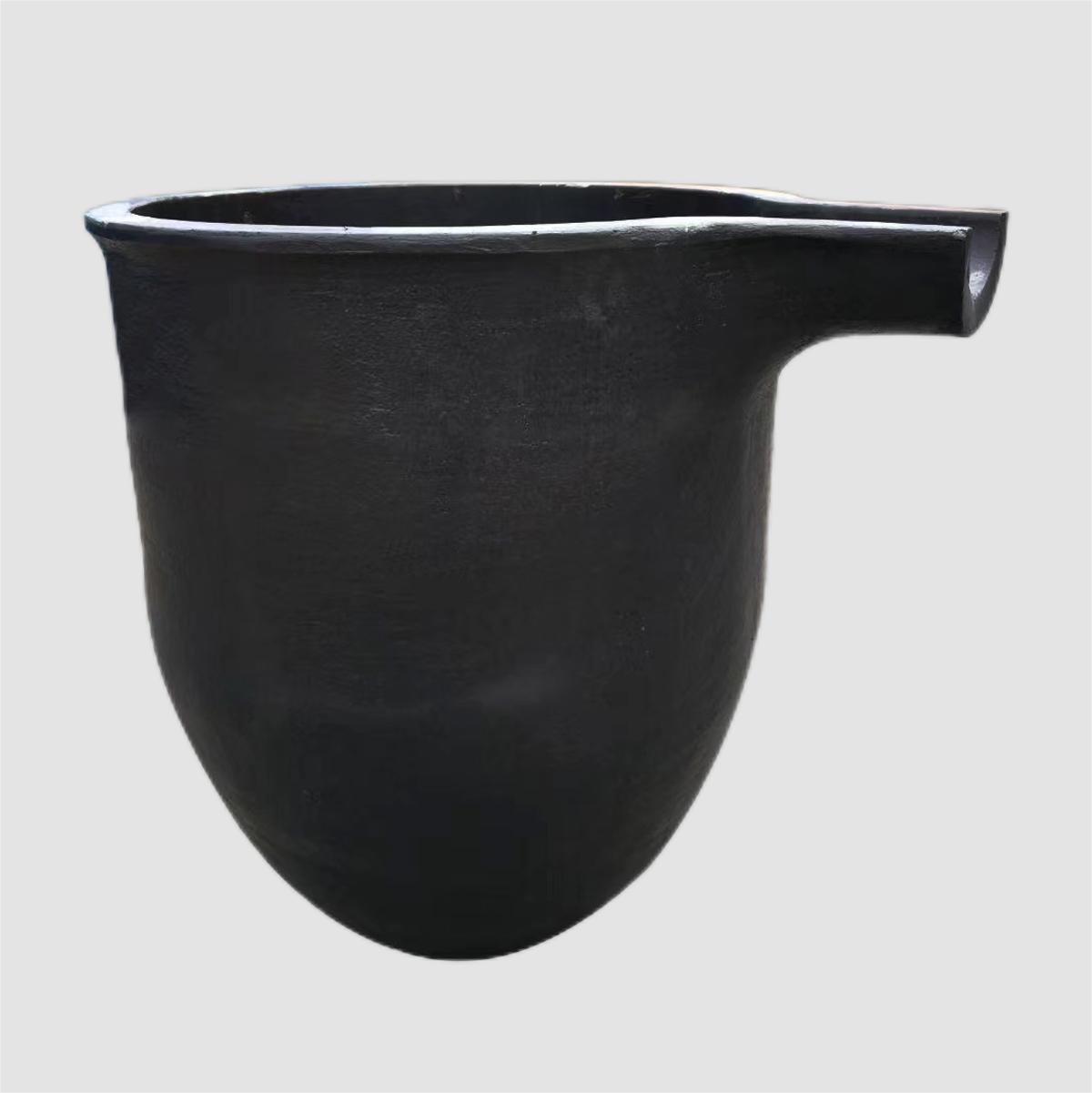
1.4 Secondary grinding
The paste is crushed, ground, and sieved into particles of tens to hundreds of micrometers in size before being mixed evenly. It is used as a pressing material, called pressing powder. The equipment for secondary grinding usually uses a vertical roller mill or ball mill.
1.5 Forming
Unlike ordinary extrusion and molding, isostatic pressing graphite is formed using cold isostatic pressing technology (Figure 2). Fill the raw material powder into the rubber mold, and compact the powder through high-frequency electromagnetic vibration. After sealing, vacuum the powder particles to exhaust the air between them. Place it in a high-pressure container containing liquid media such as water or oil, pressurize it to 100-200MPa, and press it into a cylindrical or rectangular product.
According to Pascal's principle, pressure is applied to a rubber mold through a liquid medium such as water, and the pressure is equal in all directions. In this way, the powder particles are not oriented in the filling direction in the mold, but are compressed in an irregular arrangement. Therefore, although graphite is anisotropic in crystallographic properties, overall, the isostatic pressing graphite is isotropic. The formed products not only have cylindrical and rectangular shapes, but also cylindrical and crucible shapes.
The isostatic pressing molding machine is mainly used in the powder metallurgy industry. Due to the demand of high-end industries such as aerospace, nuclear industry, hard alloys, and high-voltage electromagnetic, the development of isostatic pressing technology is very fast, and it has the ability to manufacture cold isostatic pressing machines with a working cylinder inner diameter of 3000mm, a height of 5000mm, and a maximum working pressure of 600MPa. At present, the maximum specifications of cold isostatic pressing machines used in the carbon industry for producing isostatic pressing graphite are Φ 2150mm × 4700mm, with a maximum working pressure of 180MPa.
1.6 Baking
During the roasting process, a complex chemical reaction occurs between the aggregate and the binder, causing the binder to decompose and release a large amount of volatile matter, while also undergoing a condensation reaction. In the low-temperature preheating stage, the raw product expands due to heating, and in the subsequent heating process, the volume shrinks due to condensation reaction.
The larger the volume of the raw product, the more difficult it is to release volatile matter, and the surface and interior of the raw product are prone to temperature differences, uneven thermal expansion and contraction, which may lead to cracks in the raw product.
Due to its fine structure, isostatic pressing graphite requires a particularly slow roasting process, and the temperature inside the furnace should be very uniform, especially during the temperature stage where asphalt volatiles are rapidly discharged. The heating process should be carried out with caution, with a heating rate not exceeding 1 ℃/h and a temperature difference within the furnace of less than 20 ℃. This process takes about 1-2 months.
1.7 Impregnation
During roasting, the volatile matter of coal tar pitch is discharged. Fine pores are left in the product during gas discharge and volume contraction, almost all of which are open pores.
In order to improve the volume density, mechanical strength, conductivity, thermal conductivity, and chemical resistance of the product, the pressure impregnation method can be used, which involves impregnating coal tar pitch into the interior of the product through open pores.
The product needs to be preheated first, and then vacuumed and degassed in the impregnation tank. Then, the melted coal tar asphalt is added to the impregnation tank and pressurized to allow the impregnating agent asphalt to enter the interior of the product. Usually, isostatic pressing graphite undergoes multiple cycles of impregnation roasting.
1.8 Graphitization
Heat the calcined product to about 3000 ℃, arrange the lattice of carbon atoms in an orderly manner, and complete the transformation from carbon to graphite, which is called graphitization.
The graphitization methods include Acheson method, internal thermal series connection method, high-frequency induction method, etc. The usual Acheson process takes approximately 1-1.5 months for products to be loaded and discharged from the furnace. Each furnace can handle several tons to dozens of tons of roasted products.
Post time: Sep-29-2023