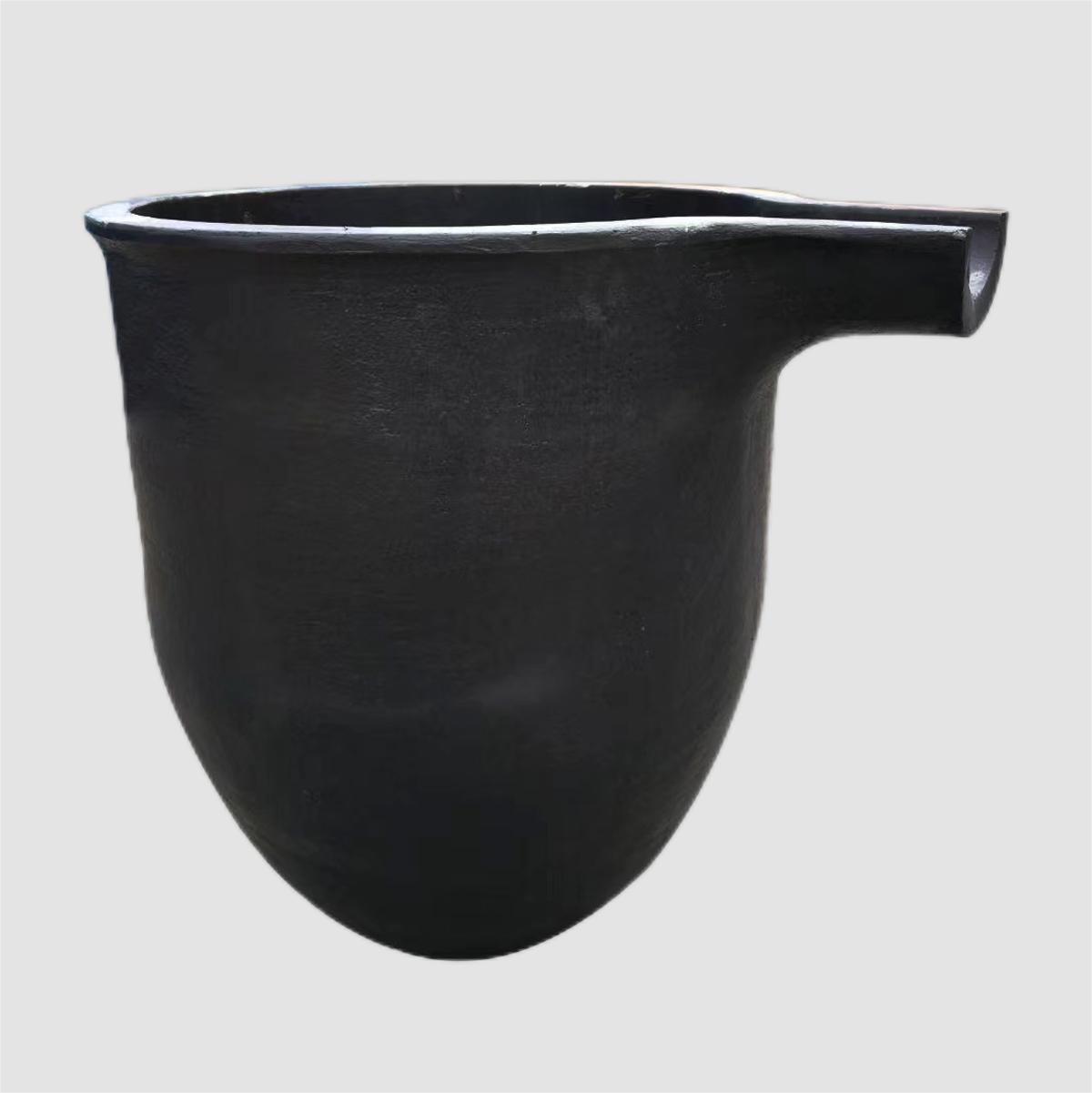
Isostatic pressing graphite is a new type of graphite material developed in the 1960s, which has a series of excellent properties. For example, isostatic pressing graphite has good heat resistance. In an inert atmosphere, its mechanical strength not only does not decrease with the increase of temperature, but also increases, reaching its highest value at around 2500 ℃; Compared with ordinary graphite, its structure is fine and dense, and its uniformity is good; The coefficient of thermal expansion is very low and has excellent thermal shock resistance; Isotropic; Strong chemical corrosion resistance, good thermal and electrical conductivity; Has excellent mechanical processing performance.
It is precisely because of its excellent performance that isostatic pressing graphite is widely used in fields such as metallurgy, chemistry, electrical, aerospace, and atomic energy industry. Moreover, with the development of science and technology, the application fields are constantly expanding.
Production process of isostatic pressing graphite
The production process of isostatic pressing graphite is shown in Figure 1. It is obvious that the production process of isostatic pressing graphite is different from that of graphite electrodes.
Isostatic pressing graphite requires structurally isotropic raw materials, which need to be ground into finer powders. Cold isostatic pressing forming technology needs to be applied, and the roasting cycle is very long. In order to achieve the target density, multiple impregnation roasting cycles are required, and the graphitization cycle is much longer than that of ordinary graphite.
Another method for producing isostatic pressing graphite is to use mesophase carbon microspheres as raw materials. Firstly, the mesophase carbon microspheres are subjected to oxidation stabilization treatment at higher temperatures, followed by isostatic pressing, followed by further calcination and graphitization. This method is not introduced in this article.
1.1 Raw materials
The raw materials for producing isostatic pressing graphite include aggregates and binders. Aggregates are usually made from petroleum coke and asphalt coke, as well as ground asphalt coke. For example, the AXF series isostatic graphite produced by POCO in the United States is made from ground asphalt coke Gilsontecoke.
In order to adjust product performance according to different uses, carbon black and artificial graphite are also used as additives. In general, petroleum coke and asphalt coke need to be calcined at 1200~1400 ℃ to remove moisture and volatile matter before use.
However, in order to improve the mechanical properties and structural density of products, there are also direct production of isostatic pressing graphite using raw materials such as coke. The characteristic of coking is that it contains volatile matter, has self sintering properties, and expands and contracts synchronously with the binder coke. The binder usually uses coal tar pitch, and according to the different equipment conditions and process requirements of each enterprise, the softening point of coal tar pitch used ranges from 50 ℃ to 250 ℃.
The performance of isostatic pressing graphite is greatly affected by the raw materials, and the selection of raw materials is a key link in producing the required final product. Before feeding, the characteristics and uniformity of the raw materials must be strictly checked.
1.2 Grinding
The aggregate size of isostatic pressing graphite is usually required to reach below 20um. Currently, the most refined isostatic pressing graphite has a maximum particle diameter of 1 μ m. It is very thin.
To grind aggregate coke into such fine powder, an ultra-fine crusher is needed. Grinding with an average particle size of 10-20 μ The powder of m requires the use of a vertical roller mill, with an average particle size of less than 10 μ The powder of m requires the use of an air flow grinder.
1.3 Mixing and kneading
Put the ground powder and coal tar pitch binder in proportion into a heating mixer for kneading, so that a layer of asphalt is evenly adhered to the surface of the powder coke particles. After kneading, remove the paste and let it cool.
Post time: Sep-27-2023