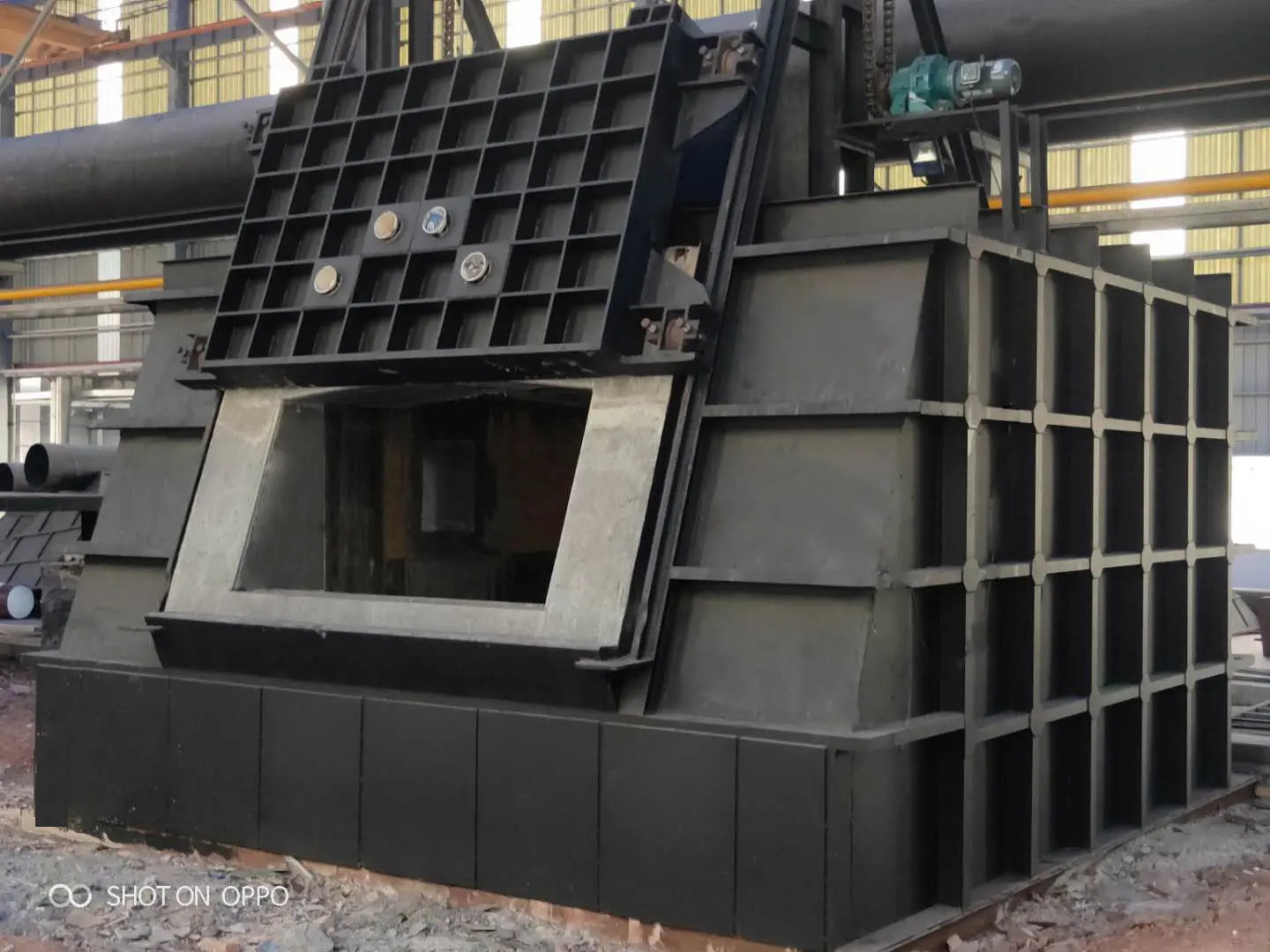
In the field of aluminum smelting, a breakthrough innovation has emerged - the reverberatory furnace. This efficient, energy-saving furnace was developed to meet the stringent requirements of the aluminum smelting process. This game-changing technology can ensure alloy composition accuracy, adapt to intermittent production, and provide large capacity in a single furnace. It is designed to reduce consumption, minimize burning loss, improve product quality, reduce labor intensity, improve labor conditions, and increase production efficiency. overall productivity. Join us as we explore the huge potential of reverberatory furnaces to transform the aluminum industry.
The reverberatory furnace is a revolutionary invention that optimizes the aluminum smelting process. The furnace uses advanced technology to reduce energy consumption while maximizing heat transfer efficiency. With its clever design, it effectively reduces heat loss, resulting in significant energy savings. Reducing energy consumption not only results in cost savings for manufacturers, but also contributes to a greener, more sustainable aluminum industry.
One of the outstanding features of the reverberatory furnace is its ability to meet strict alloy composition requirements. This precise control ensures the production of high-quality aluminum products that meet the needs of various industries. The furnace's advanced control and automation features allow for precise temperature regulation, significantly reducing alloy composition variations. This means improved product consistency, improved customer satisfaction and enhanced market competitiveness.
The reverberatory furnace has the practical advantage of being able to operate intermittently, making it very suitable for scenarios with intermittent production requirements. Unlike continuous production furnaces, reverberatory furnaces offer greater flexibility in adapting to different needs. Additionally, with its larger single furnace capacity, manufacturers can process more aluminum, increasing production efficiency and streamlining operations. This feature has proven particularly beneficial for manufacturers with fluctuating production rates, ensuring optimal utilization of resources.
By integrating advanced automation and control systems into the reverberatory furnace, labor can be significantly reduced. Operators can remotely supervise operations, minimizing manual labor and exposure to hazardous environments. This not only improves worker safety but also improves overall working conditions. Automation also streamlines production processes, reduces labor intensity, and enables manufacturers to reallocate their workforce to more value-added tasks.
Reverberatory furnaces are a game changer for the aluminum smelting industry. Its high efficiency, energy-saving capabilities, precise control of alloy composition, ability to operate intermittently, and automated features make it a truly remarkable technological advance. The furnace not only improves the quality of aluminum products, but also reduces consumption, optimizes labor use and improves overall production efficiency. With its enormous potential to transform the aluminum industry, the reverberatory furnace is undoubtedly a torchbearer for progress in the smelting world.
Post time: Nov-04-2023