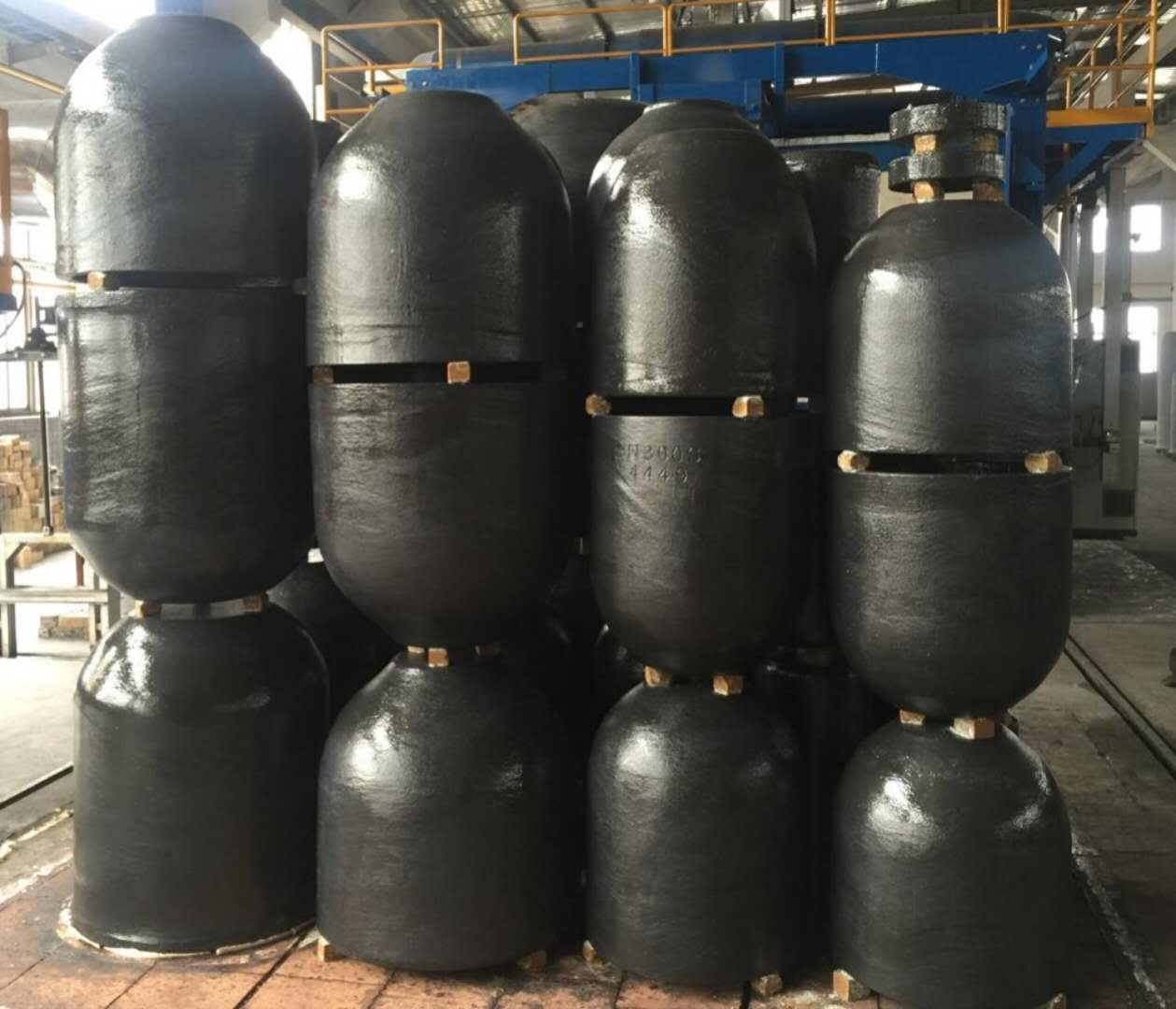
Problem 1: Holes and Gaps
1.The appearance of large holes on the walls of the crucible that have not yet thinned is mostly caused by heavy blows, such as throwing ingots into the crucible or blunt impact when cleaning up residue
2.Small holes are usually caused by cracks and require suspension of use and searching for cracks.
Problem 2: Corrosion
1.The corrosion of the metal page position inside the crucible is caused by additives and metal oxides floating on the metal surface.
2.Corrosion in multiple places inside the crucible is usually caused by corrosive substances. For example, adding additives or directly spraying additives on the crucible wall when the casting material is not added or melted.
3.Corrosion at the bottom or bottom edge of the crucible is caused by fuel and slag. The use of inferior fuel or excessively high heating temperature can cause damage to the crucible.
4.The concave additives on the surface of the crucible infiltrate and erode the outer wall of the crucible with higher temperature through the inner wall of the crucible.
Problem 3: Synthesis Problem
1.The network cracks on the surface are like crocodile skin, usually due to being too old and reaching the service life of the crucible
2.The melting speed of the casting material slows down
(1) The crucible is not preheated and baked according to the standard procedure
(2) Slag accumulation inside the crucible
(3) The crucible has reached its service life
3. Glaze detachment
(1) Place the cooled crucible directly in a hot crucible furnace for heating
(2) Heating up too quickly during heating
(3) Wet crucible or furnace
4. When there are foreign objects sticking to the bottom of the crucible, if the crucible is placed on a hard ground, it will cause the bottom of the crucible to protrude upwards and produce cracks.
5. Cracking at the bottom, thick metal slag inside the crucible caused by slag expansion.
6. The surface of the crucible turns green and begins to soften.
(1) During copper melting, the slag on the surface of the copper water overflows onto the outer wall of the crucible.
(2) Due to prolonged operation at around 1600 degrees Celsius
7. The bottom or lower edge of the new crucible is detached from the crucible and quickly heated after being damp.
8. Crucible deformation. Different parts of the crucible may experience uneven expansion when heated at excessively uneven temperatures. Please do not heat the crucible rapidly or unevenly
9. Rapid oxidation
(1) The crucible is in an oxidation atmosphere between 315 ° C and 650 ° C for a long time
(2) Improper operation during lifting or moving, resulting in damage to the glaze layer of the crucible.
(3) Unsealed between the crucible mouth and the furnace edge cover in gas or particle furnaces.
10. The wall of the crucible has become thinner and reached its service life, and it should be stopped from use.
11. The metal material added during the explosion of the crucible in use was not dried.
Post time: Sep-18-2023