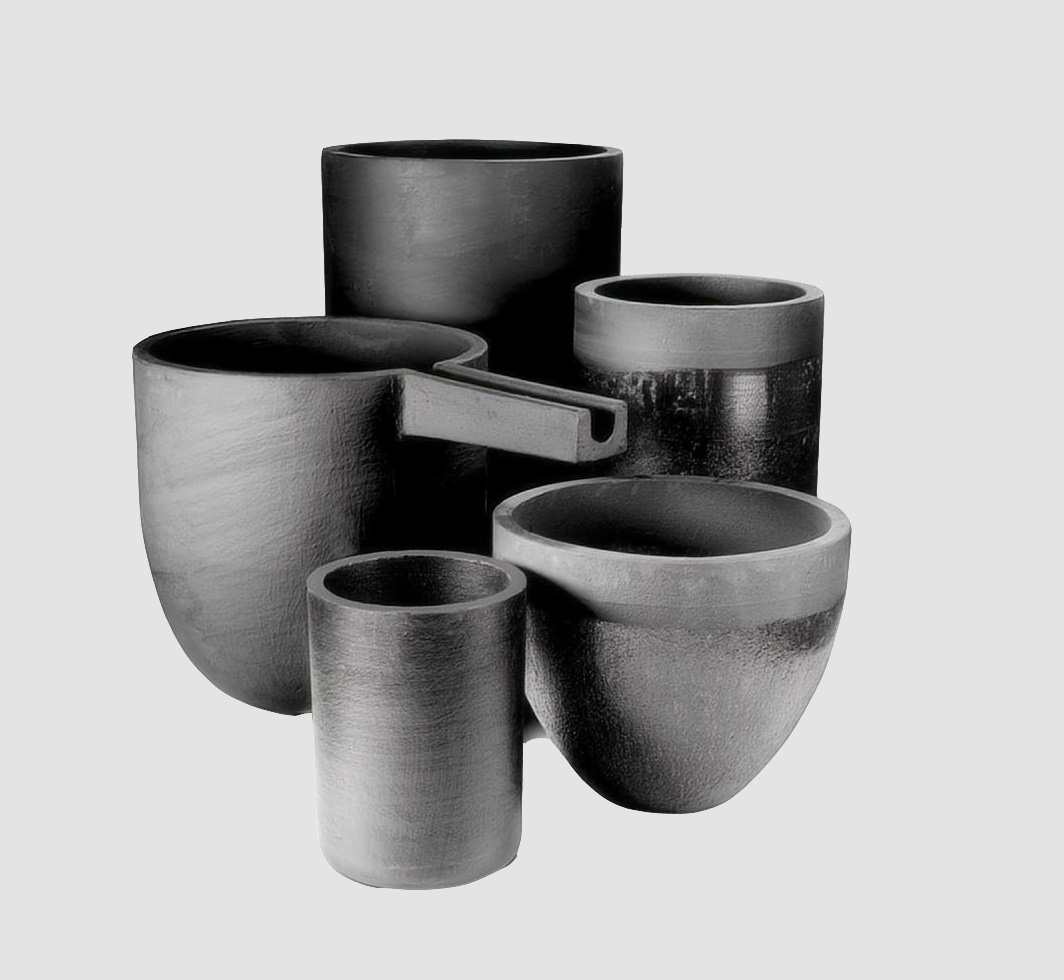
Introduction: Isostatic pressing technology is a cutting-edge method that utilizes a closed high-pressure container to shape products under ultra-high pressure conditions, ensuring uniformity in all directions. This article delves into the principles, advantages, and applications of isostatic pressing, highlighting its significance in various industries.
Principles of Isostatic Pressing: Isostatic pressing operates on Pascal's law, allowing pressure within a closed container to be evenly transmitted in all directions, be it through liquids or gases.
Advantages of Isostatic Pressing:
- High Density: Isostatic pressing achieves high-density powder products, with a density exceeding 99.9% for hot isostatic pressing items.
- Uniform Density Distribution: The pressing process ensures uniform density distribution, enabling both unidirectional and bidirectional pressing.
- Large Aspect Ratio: Capable of producing products with a high length-to-diameter ratio.
- Complex Shape Manufacturing: Ideal for producing intricate and near-net-shaped parts, resulting in high material utilization.
- Superior Product Performance: The technology produces products with low porosity, reaching as low as 0-0.00001%.
- Low Temperature Processing: The low-temperature, high-pressure process prevents grain growth, contributing to superior product performance.
- Handling Toxic Materials: Isostatic pressing is advantageous for processing toxic materials by encapsulating them.
- Environmental Friendly: Minimal or no use of additives reduces pollution, simplifies the manufacturing process, and is environmentally friendly.
Disadvantages:
- Costly Equipment: The initial investment for isostatic pressing equipment is relatively high.
- Complex Coating Techniques: Coating the workpieces involves intricate processes, demanding strict air-tightness, material selection, and precise fabrication.
- Low Processing Efficiency: Isostatic pressing has a lower processing efficiency, with extended cycles, especially in hot isostatic pressing that can take up to 24 hours.
Applications:
- Powder Material Forming: Isostatic pressing finds extensive applications in shaping powder materials.
- Hot Isostatic Pressing (HIP) in Powder Metallurgy: Particularly used in the production of powder metallurgy products.
- Casting Defect Treatment: Effective in treating defects like porosity, cracks, shrinkage, and closure in castings.
- Material Bonding: Isostatic pressing is applied in bonding heterogeneous materials.
Conclusion: Isostatic pressing technology, despite its initial investment and processing time drawbacks, proves to be a highly valuable technique for producing high-density, intricately shaped, and superior-performance products across various industries. As technology advances, the advantages of isostatic pressing are likely to outweigh its disadvantages, making it an increasingly integral part of modern manufacturing processes.
Post time: Jan-10-2024