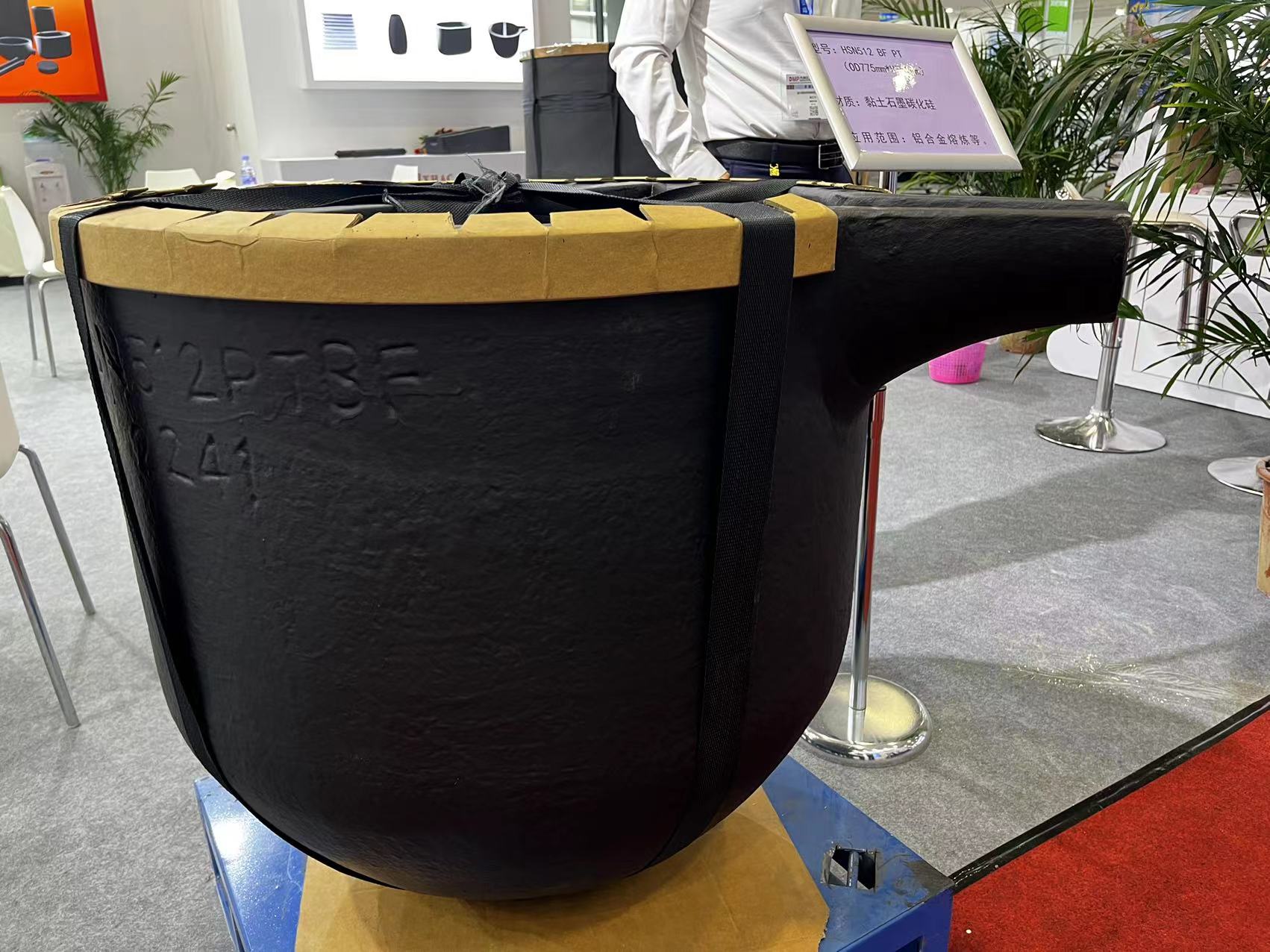
The preparation method of high-strength graphite silicon carbide crucible for metal smelting includes the following steps: 1) raw material preparation; 2) primary mixing; 3) material drying; 4) crushing and screening; 5) secondary material preparation; 6) secondary mixing; 7) pressing and molding; 8) cutting and trimming; 9) drying; 10) glazing; 11) primary firing; 12) impregnation; 13) secondary firing; 14) coating; 15) finished product. The crucible produced using this new formula and production process has strong high-temperature resistance and corrosion resistance. The average lifespan of the crucible reaches 7-8 months, with a uniform and defect-free internal structure, high strength, thin walls, and good thermal conductivity. Additionally, the glaze layer and coating on the surface, along with multiple drying and firing processes, significantly improve the product's corrosion resistance and reduce energy consumption by approximately 30%, with a high degree of vitrification.
This method involves the field of non-ferrous metallurgy casting, especially the preparation method of high-strength graphite silicon carbide crucible for metal smelting.
[Background Technology] Special graphite silicon carbide crucibles are mainly used in non-ferrous metal casting and forging processes, as well as in the recovery and refining of precious metals, and the production of high-temperature and corrosion-resistant products required for plastics, ceramics, glass, cement, rubber, and pharmaceutical manufacturing, as well as corrosion-resistant containers required in the petrochemical industry.
Existing special graphite silicon carbide crucible formulations and production processes produce products with an average lifespan of 55 days, which is too short. The use and production costs continue to increase, and the amount of waste generated is also high. Therefore, researching a new type of special graphite silicon carbide crucible and its production process is an urgent problem to solve, as these crucibles have significant applications in various industrial chemical fields.
[0004]To address the above problems, a method for preparing high-strength graphite silicon carbide crucibles for metal smelting is provided. Products prepared according to this method are resistant to high temperatures and corrosion, have a long service life, and achieve energy savings, emission reduction, environmental protection, and high recycling rate of waste during production, maximizing the circulation and utilization of resources.
The preparation method of high-strength graphite silicon carbide crucibles for metal smelting includes the following steps:
- Raw material preparation: Silicon carbide, graphite, clay, and metallic silicon are placed in their respective ingredient hoppers by crane, and PLC program automatically controls the discharge and weighing of each material according to the required ratio. Pneumatic valves control the discharge, and at least two weighing sensors are set at the bottom of each ingredient hopper. After weighing, the materials are placed in a mixing machine by an automatic movable cart. The initial addition of silicon carbide is 50% of its total amount.
- Secondary mixing: After the raw materials are mixed in the mixing machine, they are discharged into a buffer hopper, and the materials in the buffer hopper are lifted to the mixing hopper by a bucket elevator for secondary mixing. An iron removal device is set at the discharge port of the bucket elevator, and a water addition device is set above the mixing hopper to add water while stirring. The water addition rate is 10L/min.
- Material drying: The wet material after mixing is dried in a drying equipment at a temperature of 120-150°C to remove moisture. After complete drying, the material is taken out for natural cooling.
- Crushing and screening: The dried clumped material enters a crushing and screening equipment for pre-crushing, then enters a counterattack crusher for further crushing, and simultaneously passes through a 60-mesh screening equipment. Particles larger than 0.25mm are returned for recycling for further pre-crushing, crushing, and screening, while particles smaller than 0.25mm are sent to a hopper.
- Secondary material preparation: The materials in the discharge hopper are transported back to the batching machine for secondary preparation. The remaining 50% of silicon carbide is added during the secondary preparation. The materials after the secondary preparation are sent to the mixing machine for re-mixing.
- Secondary mixing: During the secondary mixing process, a special solution with viscosity is added to the mixing hopper through a special solution adding device with a specific gravity. The special solution is weighed by a weighing bucket and added to the mixing hopper.
- Pressing and molding: The materials after the secondary mixing are sent to an isostatic pressing machine hopper. After loading, compaction, vacuuming, and cleaning in the mold, the materials are pressed in the isostatic pressing machine.
- Cutting and trimming: This includes cutting the height and trimming the crucible burrs. Cutting is done by a cutting machine to cut the crucible to the required height, and the burrs after cutting are trimmed.
- Drying: The crucible, after being cut and trimmed in step (8), is sent to a drying oven for drying, with a drying temperature of 120-150°C. After drying, it is kept warm for 1-2 hours. The drying oven is equipped with an air duct adjustment system, which consists of several adjustable aluminum plates. These adjustable aluminum plates are arranged on the two inner sides of the drying oven, with an air duct between every two aluminum plates. The gap between every two aluminum plates is adjusted to regulate the air duct.
- Glazing: The glaze is made by mixing glaze materials with water, including bentonite, refractory clay, glass powder, feldspar powder, and sodium carboxymethyl cellulose. The glaze is applied manually with a brush during glazing.
- Primary firing: The crucible with applied glaze is fired once in a kiln for 28-30 hours. To improve firing efficiency, a labyrinth kiln bed with a sealing effect and air blockage is set on the bottom of the kiln. The kiln bed has a bottom layer of sealing cotton, and above the sealing cotton, there is a layer of insulation brick, forming a labyrinth kiln bed.
- Impregnation: The fired crucible is placed in an impregnation tank for vacuum and pressure impregnation. The impregnation solution is transported to the impregnation tank through a sealed pipeline, and the impregnation time is 45-60 minutes.
- Secondary firing: The impregnated crucible is placed in a kiln for secondary firing for 2 hours.
- Coating: The crucible after secondary firing is coated with a water-based acrylic resin paint on the surface.
- Finished product: After the coating is completed, the surface is dried, and after drying, the crucible is packaged and stored.
Post time: Mar-20-2024