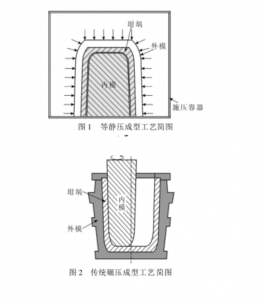
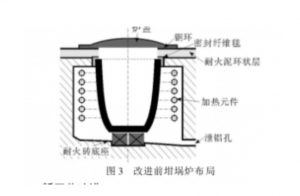
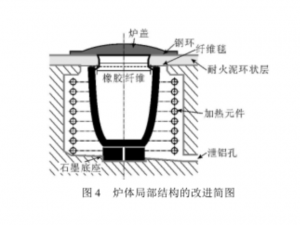
Graphite crucible production has evolved significantly with the advent of isostatic pressing technology, marking it as the most advanced technique globally. In comparison to traditional ramming methods, isostatic pressing results in crucibles with uniform texture, higher density, energy efficiency, and superior resistance to oxidation. The application of high pressure during molding significantly enhances the crucible's texture, reducing porosity and subsequently boosting thermal conductivity and corrosion resistance, as illustrated in Figure 1. In an isostatic environment, each part of the crucible experiences uniform molding pressure, ensuring material consistency throughout. This method, as depicted in Figure 2, outperforms the traditional ramming process, leading to a substantial improvement in crucible performance.
1. Problem Statement
A concern arises in the context of an aluminum alloy insulation resistance wire crucible furnace using rammed graphite crucibles, with a lifespan of approximately 45 days. After only 20 days of use, a noticeable decline in thermal conductivity is observed, accompanied by micro-cracks on the crucible's outer surface. In the later stages of use, a severe drop in thermal conductivity is evident, rendering the crucible nearly non-conductive. Additionally, multiple surface cracks develop, and discoloration occurs at the crucible's top due to oxidation.
Upon inspecting the crucible furnace, as shown in Figure 3, a base composed of stacked refractory bricks is utilized, with the bottommost heating element of the resistance wire situated 100 mm above the base. The crucible's top is sealed using asbestos fiber blankets, positioned around 50 mm from the outer edge, revealing significant abrasion on the inner edge of the crucible's top.
2. New Technological Improvements
Improvement 1: Adoption of Isostatic Pressed Clay Graphite Crucible (with Low-Temperature Oxidation Resistant Glaze)
The utilization of this crucible significantly enhances its application in aluminum alloy insulation furnaces, particularly in terms of oxidation resistance. Graphite crucibles typically oxidize at temperatures above 400 ℃, while the insulation temperature of aluminum alloy furnaces ranges between 650 and 700 ℃. Crucibles with low-temperature oxidation-resistant glaze can effectively slow down the oxidation process at temperatures above 600 ℃, ensuring prolonged excellent thermal conductivity. Simultaneously, it prevents strength reduction due to oxidation, extending the crucible's lifespan.
Improvement 2: Furnace Base Utilizing Graphite of the Same Material as the Crucible
As depicted in Figure 4, using a graphite base of the same material as the crucible ensures uniform heating of the crucible's bottom during the heating process. This mitigates temperature gradients caused by uneven heating and reduces the tendency for cracks resulting from uneven bottom heating. The dedicated graphite base also guarantees stable support for the crucible, aligning with its bottom and minimizing stress-induced fractures.
Improvement 3: Local Structural Enhancements of the Furnace (Figure 4)
- Improved inner edge of the furnace cover, effectively preventing wear on the crucible's top and significantly enhancing furnace sealing.
- Ensuring the resistance wire is level with the crucible's bottom, guaranteeing sufficient bottom heating.
- Minimizing the impact of top fiber blanket seals on crucible heating, ensuring adequate heating at the crucible's top and reducing the effects of low-temperature oxidation.
Improvement 4: Refining Crucible Usage Processes
Before usage, preheat the crucible in the furnace at temperatures below 200 ℃ for 1-2 hours to eliminate moisture. After preheating, rapidly raise the temperature to 850-900 ℃, minimizing dwell time between 300-600 ℃ to reduce oxidation within this temperature range. Subsequently, lower the temperature to the working temperature and introduce aluminum liquid material for normal operation.
Due to the corrosive effects of refining agents on crucibles, follow correct usage protocols. Regular slag removal is essential and should be performed when the crucible is hot, as cleaning slag becomes challenging otherwise. Vigilant observation of the crucible's thermal conductivity and the presence of aging on the crucible walls is crucial in the later stages of use. Timely replacements should be made to avoid unnecessary energy loss and aluminum liquid leakage.
3. Improvement Results
The extended lifespan of the improved crucible is noteworthy, maintaining thermal conductivity for prolonged durations, with no surface cracking observed. User feedback indicates improved performance, not only reducing production costs but also significantly enhancing production efficiency.
4. Conclusion
- Isostatic pressed clay graphite crucibles outperform traditional crucibles in terms of performance.
- The furnace structure should match the size and structure of the crucible for optimal performance.
- Proper crucible usage significantly extends its lifespan, effectively controlling production costs.
Through meticulous research and optimization of crucible furnace technology, the enhanced performance and lifespan contribute substantively to increased production efficiency and cost savings.
Post time: Dec-24-2023