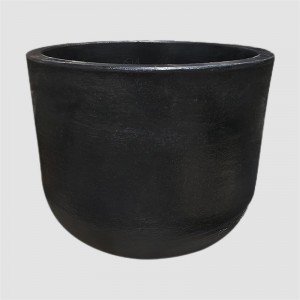
Graphite crucible is a special product that plays a vital role in the refining process of gold, silver, copper and other precious metals. Although many people may not be familiar with it, the production of graphite crucibles involves several complex stages to ensure the superior quality and mechanical strength of the final product. In this article, we will delve into the details of each stage involved in the graphite crucible manufacturing process.
The initial stages of producing graphite crucibles involve a drying process. After the crucible and its supporting pendant parts are formed, they are inspected according to semi-finished product standards. This check ensures that only qualified individuals advance to subsequent stages. After sorting, they undergo a glazing process, in which the crucible surface is coated with a glaze. This glaze layer serves several purposes, including increasing the density and mechanical strength of the crucible, ultimately improving its overall quality.
The firing stage is a critical part of the manufacturing process. It involves subjecting a graphite crucible to high temperatures in a kiln, thereby strengthening the structure of the crucible. This process is crucial to ensure the durability and reliability of the crucible during the refining process. The firing principle can be divided into four different stages to better understand the changes that occur in the crucible structure during this process.
The first stage is the preheating and firing stage, and the temperature in the kiln is maintained at about 100 to 300°C. At this stage, the remaining moisture in the crucible is gradually removed. Open the kiln's skylight and slow down the heating rate to prevent sudden temperature swings. Temperature control is crucial at this stage, as too much residual moisture can cause the crucible to crack or even explode.
The second stage is the low-temperature firing stage, with a temperature of 400 to 600°C. As the kiln continues to heat up, the bound water within the crucible begins to break down and evaporate. The main components A12O3 and SiO2, which were previously bound to the clay, begin to exist in a free state. However, it should be noted that the glaze layer on the surface of the crucible has not melted yet. To prevent any surprises, the heating rate should still be slow and steady. Rapid and uneven heating can cause the crucible to crack or collapse, compromising its integrity.
Entering the third stage, the medium temperature firing stage usually occurs between 700 and 900°C. At this stage, the amorphous Al2O3 in the clay is partially transformed to form Y-type crystalline Al2O3. This transformation further enhances the structural integrity of the crucible. It is crucial to maintain precise temperature control during this period to avoid any undesirable results.
The final stage is the high-temperature firing stage, with the temperature above 1000°C. At this point, the glaze layer finally melts, ensuring the crucible surface is smooth and sealed. Higher temperatures also contribute to the overall improvement in the crucible's mechanical strength and durability.
All in all, the production process of graphite crucibles involves several meticulous stages. From drying and inspecting the semi-finished product to glazing and firing, each step is critical to ensuring the quality and reliability of the final graphite crucible. Adhering to temperature control measures and maintaining proper heating rates is critical to preventing any potential defects or accidents. The end result is a high-quality graphite crucible that can withstand the rigorous refining process of precious metals.
Post time: Nov-29-2023