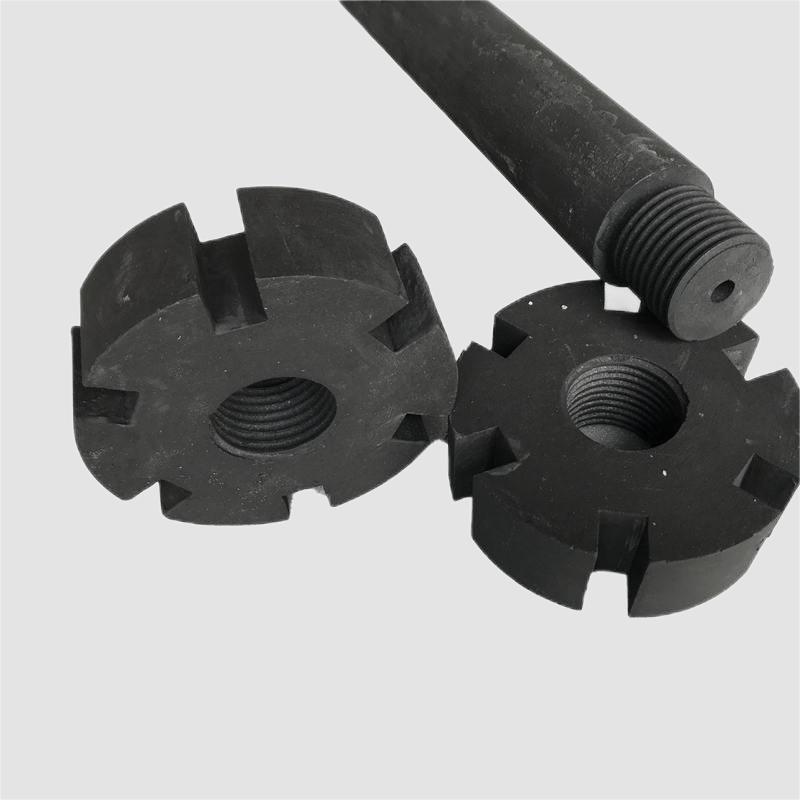
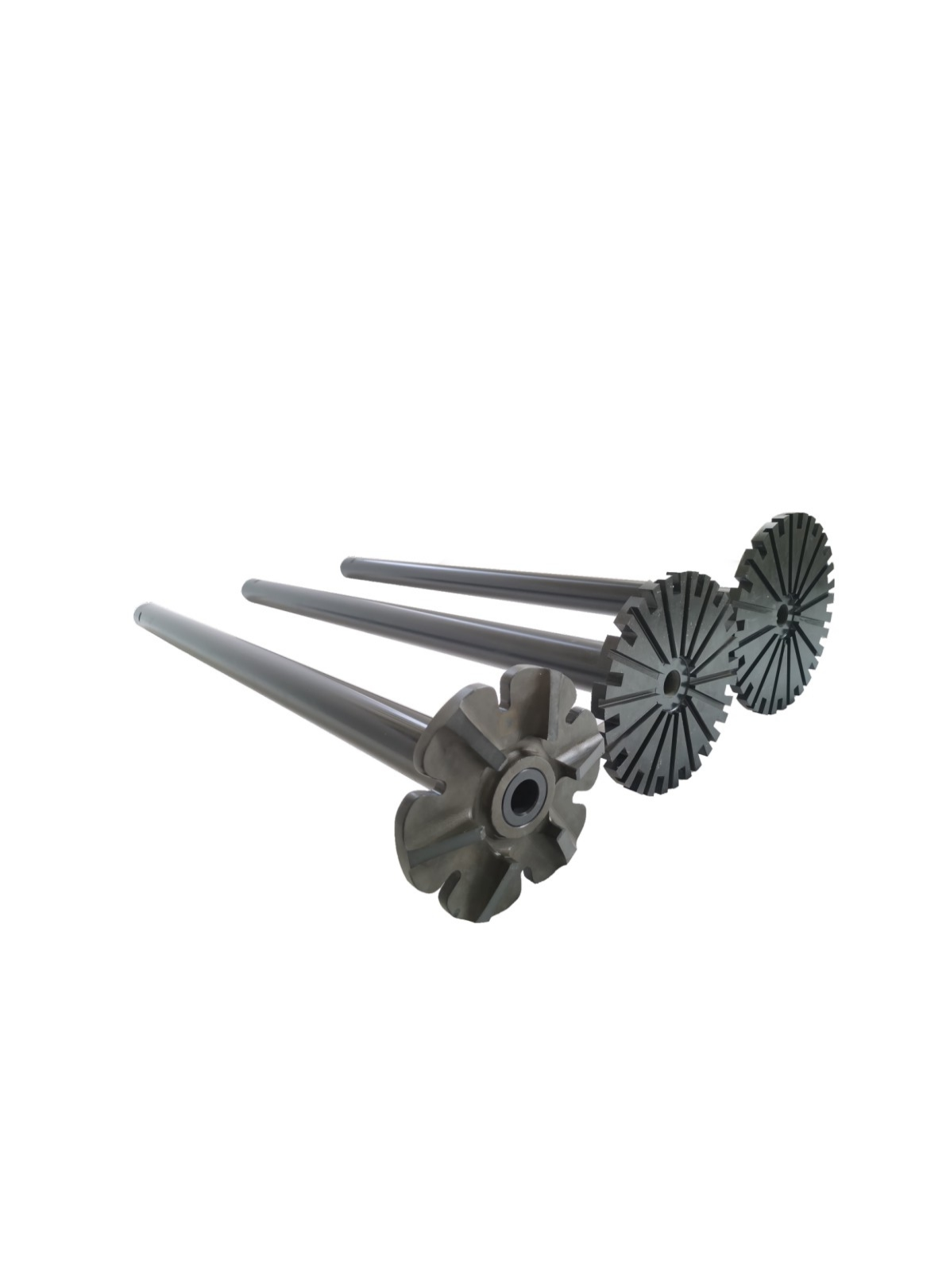
Product Introduction:
The working principle of a graphite rotor is that the rotating rotor breaks the nitrogen (or argon) blown into the aluminum melt into a large number of dispersed bubbles and disperses them in the molten metal. Bubbles in the melt absorb hydrogen from the melt based on the principle of gas partial pressure difference and surface adsorption, adsorb oxidation slag, and are carried out of the melt surface as the bubbles rise, enabling the melt to be purified. Due to the fine dispersion of bubbles, they mix evenly with the rotating melt and slowly float up in a spiral shape. They have a long contact time with the melt and do not form a continuous straight upward airflow, thereby removing harmful hydrogen from the aluminum melt and significantly improving the purification effect.
Features of graphite rotor products:
1. The graphite rotor rotating nozzle is made of high-purity graphite. 2. After surface treatment, the service life is about three times that of ordinary products, and it is widely used in the aluminum alloy casting industry.
In terms of graphite rotor economy:
For aluminum alloy foundries and aluminum product factories, it is important to reduce processing costs. In this regard, the graphite rotors produced by our company can bring the following benefits:
1. Reduce processing costs
2. Reduce the consumption of inert gases
3. Reduce the aluminum content in slag
4. Reduce labor costs
5. Performance, longer replacement cycle
6. Improve reliability and reduce maintenance costs.
Design and ordering of graphite rotors:
Due to the varying specifications of graphite rotors used on each casting or rolling production line. Firstly, the customer will provide the original design drawings and a complete on-site usage environment survey form for the graphite rotor. Then, based on the drawings, a technical analysis will be conducted combining the speed, direction of rotation, and relative position with the aluminum liquid level of the graphite rotor, and a suitable anti erosion treatment plan will be proposed.
The graphite rotor rotating nozzle is made of high-purity graphite. In addition to considering the need to disperse bubbles, the structure of the nozzle also utilizes the centrifugal force generated by stirring the aluminum alloy melt to evenly mix the melt into the nozzle with the horizontally sprayed gas, forming a gas/liquid flow to spray out, increasing the contact area and contact time between the bubbles and the aluminum alloy liquid, and improving the degassing and purification effect. The speed of the graphite rotor can be adjusted steplessly through frequency converter speed control, up to 700? R/min. The specification of graphite rotor is Φ 70mm~250mm, with impeller specifications of Φ 85mm~350mm, high-purity graphite rotor has characteristics such as high strength, high temperature resistance, and aluminum flow corrosion resistance. During the purification and degassing process, nitrogen is introduced to cover the surface of the aluminum alloy liquid inside the box for protection, keeping the exposed part of the graphite rotor in an inert gas to prevent high-temperature oxidation of the rotor and extend its service life. The impeller shape is streamlined, which can reduce the resistance during rotation, and the friction and erosion force generated between the impeller and the aluminum alloy liquid is also relatively small. This results in a degassing rate of over 50%, shortening smelting time, and reducing production costs.
Post time: Oct-04-2023