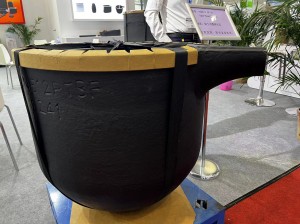
In the field of metallurgy and materials science, graphite silicon carbide crucibles play a vital role in various processes such as melting, casting and heat treatment of metals. However, the integrity of the graphite silicon carbide crucible can be affected by various factors, leading to cracks and potential failure. Understanding the causes and prevention of these cracks is critical to ensuring the efficiency and safety of industrial processes.
One common type of crack that can occur in a graphite silicon carbide crucible is a transverse crack near the bottom. These cracks usually appear due to rapid changes in temperature during preheating, tapping the bottom with a hard object, thermal expansion of the remaining metal, or impact of the cast material. A rapid increase in temperature during preheating can subject the graphite silicon carbide crucible to thermal stress, leading to the formation of cracks. Additionally, hitting the bottom with a hard object or hitting the casting material can weaken the graphite silicon carbide crucible's structural integrity, making it susceptible to breakage.
Another type of transverse crack can occur about halfway up the graphite silicon carbide crucible and is usually attributed to placing the graphite silicon carbide crucible on an inappropriate base, applying too much force in the clamping position of the graphite silicon carbide crucible tongs, or incorrect burner control resulting in uneven heating . Placing the graphite silicon carbide crucible on an inappropriate base can create stress points that can lead to cracks. Similarly, excessive force in the clamping position of the graphite silicon carbide crucible clamp will exert uneven pressure on the graphite silicon carbide crucible, causing the graphite silicon carbide crucible to break. Additionally, improper burner control can lead to uneven heating, which can lead to thermal stress and crack formation.
When using a pouring graphite silicon carbide crucible with a mouth, due to improper installation, the refractory soil under the graphite silicon carbide crucible mouth is squeezed, and transverse cracks will appear in the lower part of the graphite silicon carbide crucible mouth. This misalignment can create pressure points that can cause the graphite silicon carbide crucible to crack.
In addition, longitudinal cracks running through the bottom of the lower edge of the new graphite silicon carbide crucible may be caused by the cooled graphite silicon carbide crucible being subjected to high-temperature fire or the bottom heating too quickly during the cooling process. Thermal stresses generated by these effects can cause cracks in the graphite silicon carbide crucible bottom, often accompanied by glaze peeling and other related phenomena.
To reduce the occurrence of these cracks, there are some preventive measures that can be taken. Ensuring that the temperature is controlled and gradually increased during preheating will help minimize thermal stress on the graphite silicon carbide crucible. Additionally, using proper tools and handling techniques, such as avoiding hitting the bottom with hard objects and ensuring the graphite silicon carbide crucible is installed correctly, can help prevent cracks from forming. Proper placement of the graphite silicon carbide crucible on a suitable base and careful control of clamping force will also help reduce the risk of cracks. Additionally, maintaining uniform heating and avoiding sudden changes in temperature can help prevent thermal stresses and cracks from forming in the graphite silicon carbide crucible.
In summary, understanding the causes of transverse and longitudinal cracks in graphite silicon carbide crucibles is critical to maintaining the integrity and functionality of these critical components in industrial processes. By taking appropriate precautions and handling techniques, the occurrence of these cracks can be minimized, ensuring the efficiency and safety of metallurgical operations.
Post time: Apr-16-2024